
Proper bearing lubrication is critical in ensuring optimal performance and longevity of your bearings. Effective lubrication reduces friction and wear, prevents overheating and corrosion, and minimizes maintenance costs. Conversely, poor lubrication can lead to increased failure rates, potential downtime, and higher operational expenses.
The Importance of Proper Bearing Lubrication
Bearing lubrication plays an essential role in reducing friction and wear between moving parts. This not only extends the life of the bearing but also improves its performance by minimizing resistance. In addition, well-lubricated bearings help prevent overheating and corrosion, which are common causes of bearing failure. By maintaining proper lubrication, you can significantly cut down on maintenance costs associated with premature wear and tear.
Consequences of Poor Lubrication
Poor lubrication can result in a myriad of issues, including increased failure rates of bearings. When bearings fail, it often leads to unexpected equipment downtime, disrupting operations and increasing overall operational expenses. Ensuring that your bearings are properly lubricated can help avoid these costly consequences.
Types of Lubricants for Bearings
Several types of lubricants can be used for bearings, each having unique characteristics, advantages, and limitations. Understanding these options is crucial for selecting the right lubricant for your specific application.
Grease
Grease is commonly used due to its thick consistency, which stays within the bearing housing longer than other lubricant types. It provides excellent protection against contaminants and can handle high loads at moderate speeds. However, grease may not be suitable for very high-speed applications as it can cause drag.
Oil
Oil lubricants come in various grades and viscosities suited for different operational conditions. Oils offer less resistance compared to grease, making them ideal for high-speed applications while providing effective cooling. However, oils require frequent reapplication and better sealing mechanisms to prevent leakage.
Solid Lubricants
Solid lubricants, like graphite or molybdenum disulfide, are used in extreme conditions where liquid lubricants might fail, such as high temperatures or vacuum environments. These lubricants provide a long-lasting solution but have limitations regarding their application methods and load-carrying capacity.
Methods of Lubrication
Bearings can be lubricated manually, automatically, or via relubrication intervals based on usage and environmental factors.
Manual Lubrication
When applying manual lubrication, it's vital to follow best practices, including using the right tools and equipment for accurate dispensing. Proper training ensures that the lubricant is applied uniformly and in appropriate quantities.
Automatic Lubrication Systems
Various automatic systems, such as centralized or single-point lubricators, offer consistent and efficient lubrication without manual intervention. Automation enhances reliability and can be integrated into smart systems for predictive maintenance.
Relubrication Intervals
Determining the appropriate frequency for relubrication depends on factors like bearing usage and operating environment. Regularly inspecting bearings for signs of needing relubrication—such as noise, vibration, or temperature changes—is paramount.
Factors Affecting Lubrication Effectiveness
A variety of factors influence the effectiveness of bearing lubrication, including temperature, load, speed, and contamination control.
Temperature
Temperature critically impacts lubricant viscosity and performance. High temperatures can degrade lubricants faster, whereas low temperatures can increase viscosity, affecting flow. Implementing temperature control strategies helps maintain optimal lubrication conditions.
Load and Speed
Choosing the correct type of lubricant tailored to meet specific loads and speeds can optimize performance. Adjustments in lubrication techniques ensure effective bearing operation under varying mechanical stresses.
Contamination Control
Preventing contaminants, like dirt and moisture, from entering the bearing system is crucial. Using effective seals and shields plays a pivotal role in extending the life and performance of the lubrication.
Best Practices for Bearing Lubrication
Adopting best practices for bearing lubrication involves several key steps, including proper cleaning before lubrication, using the correct amount of lubricant, and continuous monitoring and maintenance.
Proper Cleaning Before Lubrication
Before applying new lubricant, thoroughly clean the bearings to remove old grease, debris, and contaminants. Use appropriate solvents to ensure complete cleanliness, which aids in effective new lubricant adhesion.
Correct Amount of Lubricant
Applying too little lubricant can lead to insufficient protection, while over-lubrication can cause overheating and energy loss. Utilize precise measuring techniques and tools to dispense the exact required amounts.
Monitoring and Maintenance
Regular inspections and audits of bearing lubrication status should be conducted. Employ diagnostic tools and sensors to track lubricant levels and bearing condition, preemptively addressing any issues.
Common Mistakes to Avoid
Aware of some common pitfalls can help avert inefficiencies and failures. Key mistakes include mixing different lubricants, ignoring manufacturer recommendations, and neglecting environmental factors.
Mixing Different Lubricants
Mixing lubricants can lead to chemical incompatibility, causing degradation and reduced performance. Follow guidelines meticulously when transitioning between different lubricants to avoid adverse reactions.
Ignoring Manufacturer Recommendations
Manufacturers specify certain types of lubricants and methods based on extensive testing. Adhering to these recommendations ensures optimal functionality and avoids potential damage stemming from deviation.
Neglecting Environmental Factors
Understand the operating environment's impact on lubrication needs. Adapt lubrication practices to suit different conditions, mitigating risks posed by factors like humidity, dust, and temperature extremes.
Innovative Trends in Bearing Lubrication
Evolving technologies present new opportunities in bearing lubrication, including nano-lubricants and smart lubrication systems integrated with IoT.
Nano-Lubricants
Nano-lubricants incorporate nanoparticles to improve efficiency and durability. Emerging evidence suggests they offer superior friction reduction and wear resistance, proving beneficial across diverse applications.
Smart Lubrication Systems
Smart lubrication systems utilize IoT to offer predictive maintenance capabilities. Real-time data analysis enables timely interventions, enhancing overall equipment reliability and performance.
Expert Tips for Optimal Bearing Lubrication
For achieving top-notch lubrication practices, consider consulting lubricant specialists and continuously updating industry's advancements.
Consulting with Lubricant Specialists
Professionals can provide invaluable advice tailored to your specific requirements. Seeking expert input is particularly vital when setting up new systems or facing complex lubrication challenges.
Continuous Learning and Adaptation
Staying abreast of the latest industry trends and advancements through training programs and certifications empowers teams to implement cutting-edge solutions effectively.
Resources and Further Reading
Dive deeper into technical manuals, guides, and online resources dedicated to bearing lubrication. Engaging in industry forums and communities fosters practical knowledge exchange among peers.
Real-World Case Studies
Explore success stories of companies that improved their operational efficiency through proper lubrication practices. Analyzing real-world scenarios offers quantifiable benefits and valuable insights into overcoming common challenges.
Discover reliable bearings and other auto parts at the Hongda auto parts trading firm. Shop now for durable automotive solutions that cater to all your vehicle requirements.
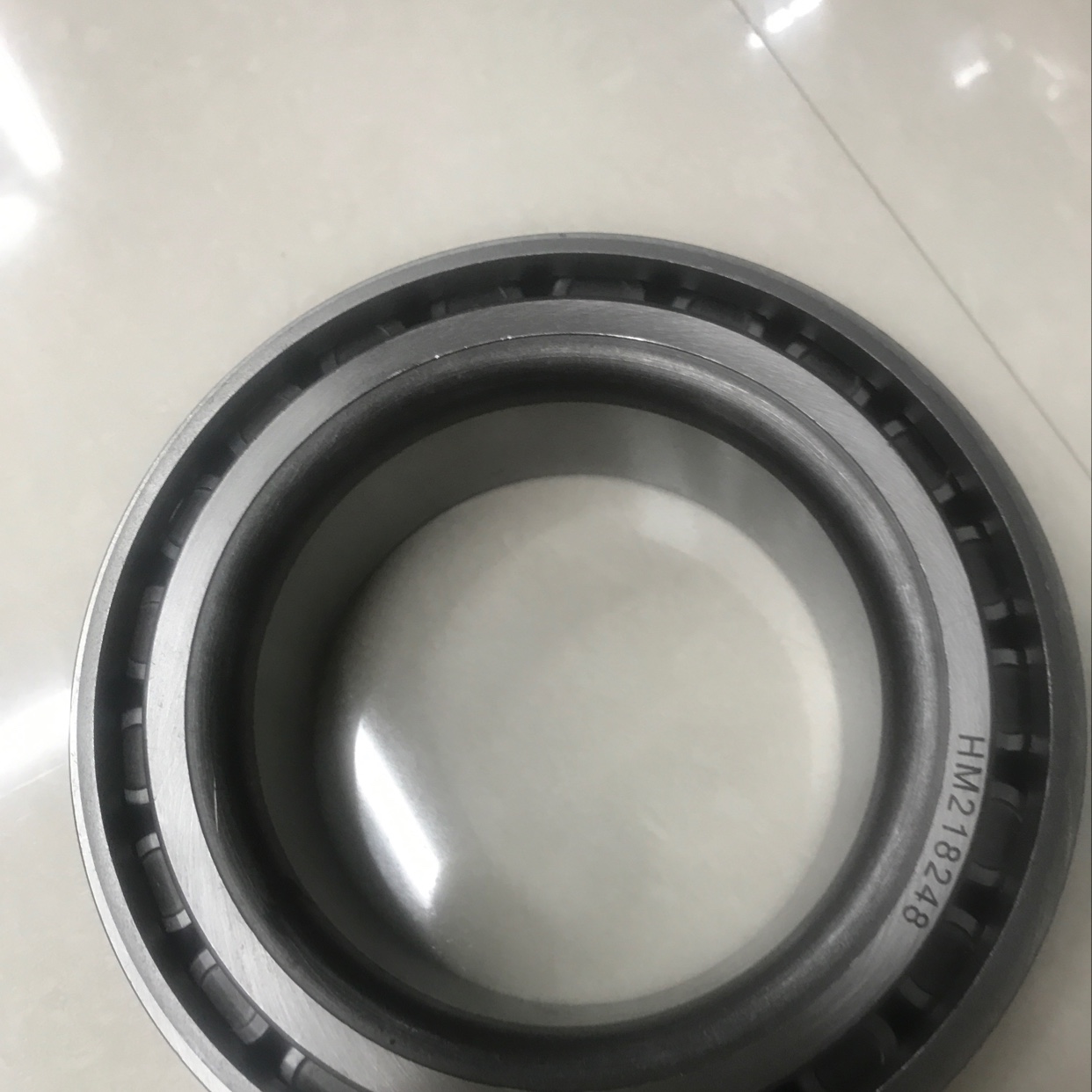
Price: $4.90
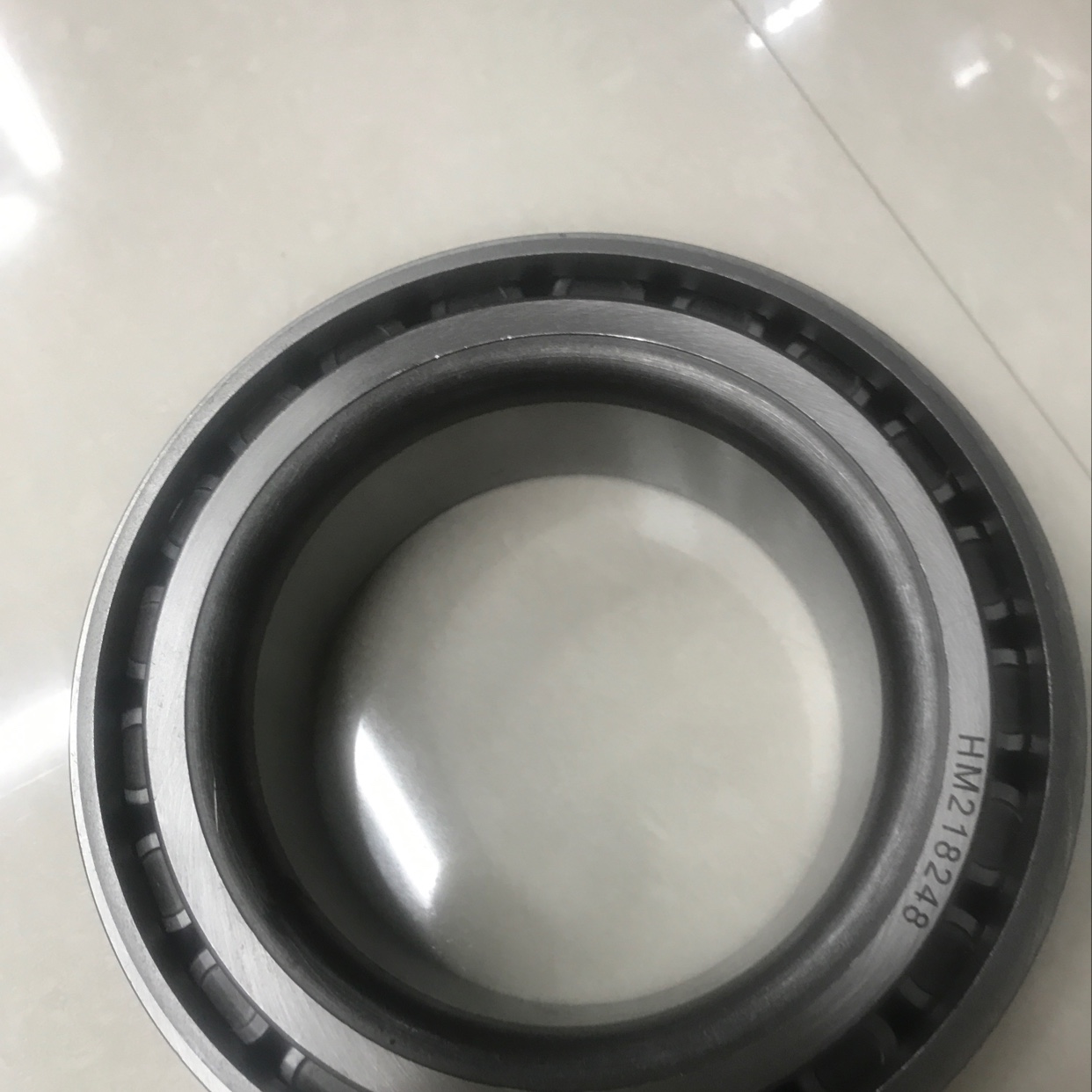